Manufacturing is experiencing a digital revolution, transforming the industry like never before. Digital transformation is driving innovation, raising consumer expectations, and reshaping how businesses operate.
Many companies are already seeing the long-term benefits of digitalisation. By adopting these changes, your business can unlock new opportunities and stay ahead in the competitive market.
This article will guide you through the Benefits, Key Challenges, and Solutions to help you successfully navigate your digital transformation journey. Whether you're looking to improve efficiency, enhance customer satisfaction, or future-proof your operations, understanding these elements will empower you to embrace digitalisation with confidence.
Key Takeaways
- The fourth industrial revolution is here, and businesses have a choice: embrace it or risk being left behind. Manufacturing firms that adopt a digital mindset stand to gain significant rewards, while those who don’t face growing risks.
- Digital transformation in manufacturing is built on five key pillars: Cloud Technology, Robotics & Automation, Artificial Intelligence (AI) & Machine Learning (ML), Internet of Things (IoT), and Data Analytics. When implemented effectively, these technologies deliver real, measurable benefits.
- However, the journey isn’t without challenges. With over 70% of digital transformation projects failing to meet their goals, it’s understandable why some hesitate. But with the right plan, skilled team, and strong support, successful digital transformation is not only possible—it’s achievable.
Understanding Digital Transformation
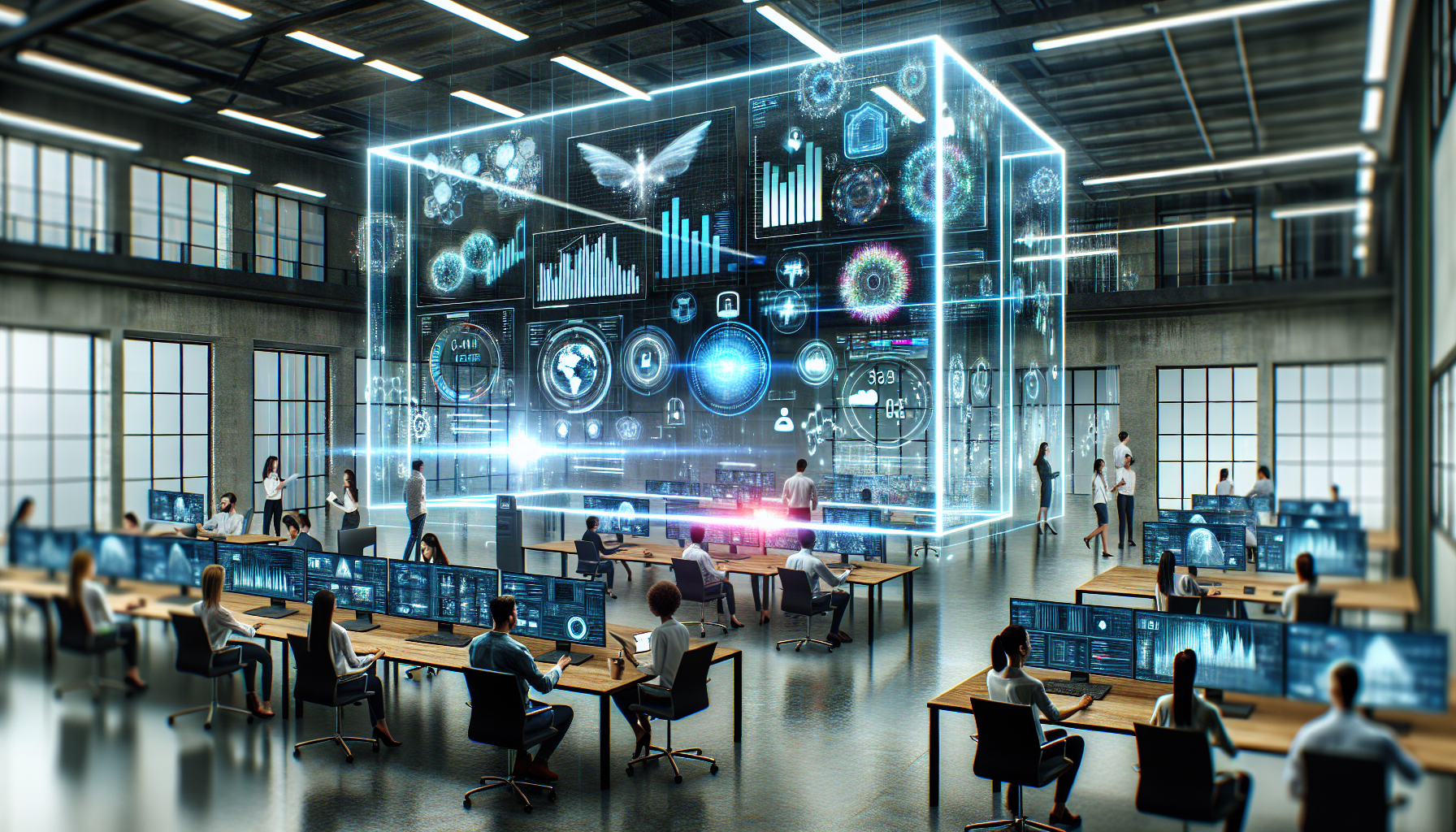
Digital transformation requires a deep re-evaluation of how businesses operate to create value and engage with stakeholders in new ways. It’s a significant shift that embeds digital technologies across all areas of the business to improve efficiency and agility. Unlike digitisation and digitalisation, which focus on specific processes, digital transformation integrates technology across the entire organisation.
In today’s fast-paced business world, staying competitive and achieving long-term success depend on embracing digital transformation. By adopting innovative practices and focusing on customer needs, businesses can stay ahead in the digital landscape.
Successful digital transformation involves collaboration across all departments and alignment with business goals. Key drivers include:
- Rising competition
- Increasing raw material and labour costs
- Growing consumer expectations
- Regulatory changes (e.g., sustainability, traceability)
- Cybersecurity concerns
Manufacturing leaders who embrace digital transformation can expect benefits such as:
- Greater operational efficiency
- Enhanced cybersecurity
- Better user experiences
- Improved data collection
- Stronger resource management
- Data-driven customer insights
These advantages contribute to a better customer experience and a stronger competitive edge.
The evolution of digital transformation in manufacturing
Manufacturing has entered the digital age, known as Industry 4.0, shifting from traditional methods to advanced, technology-driven operations. Building on the digital computing advancements of Industry 3.0, this new era integrates cyber-physical systems into manufacturing processes.
At its core is the Internet of Things (IoT), which connects machines and workflows, enabling real-time data sharing and predictive analytics. This has led to the rise of smart factories, where systems can autonomously monitor and optimise operations, boosting efficiency and minimising downtime.
Artificial Intelligence (AI) and Machine Learning (ML) further enhance manufacturing by optimising production, predicting maintenance needs, and improving quality control. Modern robotics, including collaborative robots (cobots), work alongside humans to increase productivity and safety.
Additive manufacturing, like 3D printing, has transformed prototyping and small-batch production, enabling faster innovation and customisation. Digital twins—virtual replicas of physical systems—help simulate and optimise processes, cutting development time and costs.
This digital evolution has redefined not only how products are made but also how businesses operate, creating a more agile, efficient, and customer-focused industry. As technology continues to advance, manufacturing will unlock even greater innovation and growth opportunities.
The Myth vs. Reality of Digital Transformation in the manufacturing industry
There's a myth that digital transformation complicates manufacturing, adding unnecessary layers of technology. In fact, it does the opposite—streamlining processes, improving efficiency, and enhancing product quality. Clinging to outdated methods in a digital age is like using a rowboat in a speedboat race. It's time to embrace a digitally empowered future.
Another misconception is that digital transformation can happen quickly with minimal effort. In reality, it requires time, consistent effort, and strong leadership. However, when done right, the rewards can be enormous, with returns potentially reaching 100x. Industries like retail, media, and finance show how digital transformation can drive success—or lead to failure if neglected. Manufacturing is no different: the stakes are high, but the potential is even higher.
Digital technology changing the manufacturing landscape
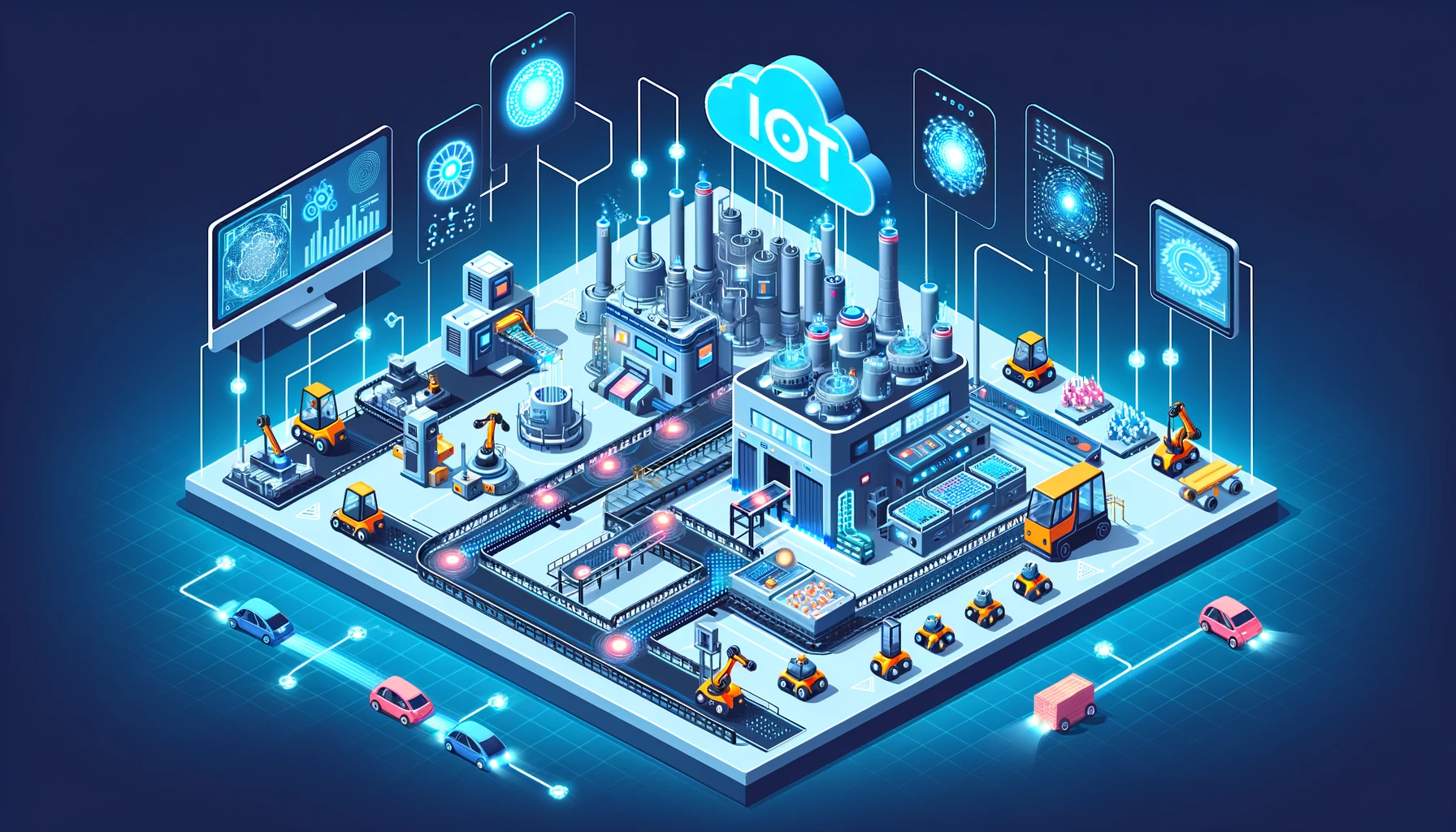
The manufacturing industry is undergoing a major transformation, fueled by powerful digital tools that make processes more efficient, flexible, and intelligent. Technologies like Cloud Computing, IoT, and AI are not just improving operations—they're revolutionising the entire industry.
Here are the key digital capabilities driving manufacturing transformation today:
Cloud Computing
Cloud technology has made powerful computing resources accessible to manufacturers of all sizes. Without requiring large upfront investments in IT infrastructure, manufacturers can now use advanced software and analytics to drive efficiency and growth.
Key Benefits of Cloud Technology:
- Streamlined Operations: Simplify supply chain management and enhance product lifecycle management.
- Cost Reduction: Lower maintenance costs and improve resource allocation.
- Innovation Support: Accelerate research and development for faster, smarter solutions.
- Agility: Quickly adapt to market demands and operational challenges with scalable, flexible systems.
Leading providers like Google, Amazon, and Microsoft are offering industry-specific accelerators tailored to manufacturing. These tools deliver best-practice solutions faster and more cost-effectively. One standout example is the Google Manufacturing Cloud, which combines efficiency, scalability, and advanced analytics to transform manufacturing processes.
Robotic and Automation
Robotics has been a key part of manufacturing for years, but digital technology has taken it to a new level. Modern robots are now more adaptable, able to learn from their environment, and work alongside humans as collaborative robots (cobots). This improves efficiency and adds flexibility, making it possible to customise products without losing speed or quality. A great example of this advancement is Figure AI.
Automation goes beyond robotics to include Business Process Automation (BPA) and Robotic Process Automation (RPA), which convert manual tasks into digital workflows. Successful automation in manufacturing requires focusing on both the back office and the factory floor. Companies that get it right can significantly cut costs and lead times, making their digital transformation efforts highly rewarding.
Artificial Intelligence & Machine Learning
AI and ML are driving digital transformation in manufacturing, offering powerful tools to analyse the vast amounts of data generated by connected devices. These technologies uncover patterns, predict outcomes, and support smarter decision-making.
AI is revolutionising manufacturing through applications like predictive maintenance, quality control, demand forecasting, and supply chain and inventory management. These innovations are reshaping traditional processes, making them more efficient and responsive.
AI-powered robots are also transforming the factory floor by working alongside humans to handle complex tasks. This collaboration boosts productivity, reduces errors, and enhances workplace safety. By leveraging these advanced technologies, manufacturers can identify and eliminate waste, creating a leaner and more efficient production environment.
Big data and analytics
Big Data and Analytics are transforming manufacturing, driving the shift toward smart factories. By processing the vast amounts of data from digital tools and IoT devices, these technologies turn complex information into actionable insights that manufacturers can use to improve performance and decision-making.
Key benefits include enhanced operational efficiency, reduced waste, optimised energy use, and improved product quality. Predictive maintenance powered by analytics minimises downtime and extends machinery life. Supply chain visibility is also greatly improved, enabling better inventory management and logistics optimisation.
Additionally, Big Data and Analytics provide valuable insights into customer preferences, supporting the move toward product customization and fostering innovation. By integrating these tools into digital manufacturing processes, the industry is advancing toward a future of greater efficiency, adaptability, and continuous improvement—where challenges are anticipated and addressed with speed and precision.
Internet of Things (IOT)
The Internet of Things (IoT), often called the industrial internet, is a cornerstone of modern manufacturing. IoT connects physical objects—such as machines, tools, and sensors—through a network that allows them to exchange data in real time without human intervention.
For example, many manufacturers use sensors embedded in production lines to monitor performance, availability, and product quality in real time. This data can be analysed to measure Overall Equipment Effectiveness (OEE), identify inefficiencies, and ultimately boost profitability.
IoT’s interconnected systems open the door to smarter, more efficient operations across industries. By enabling seamless data sharing and analysis, IoT helps manufacturers optimise processes, reduce downtime, and adapt to changing demands, paving the way for a more innovative and productive future.
Methods for Achieving Digital Excellence
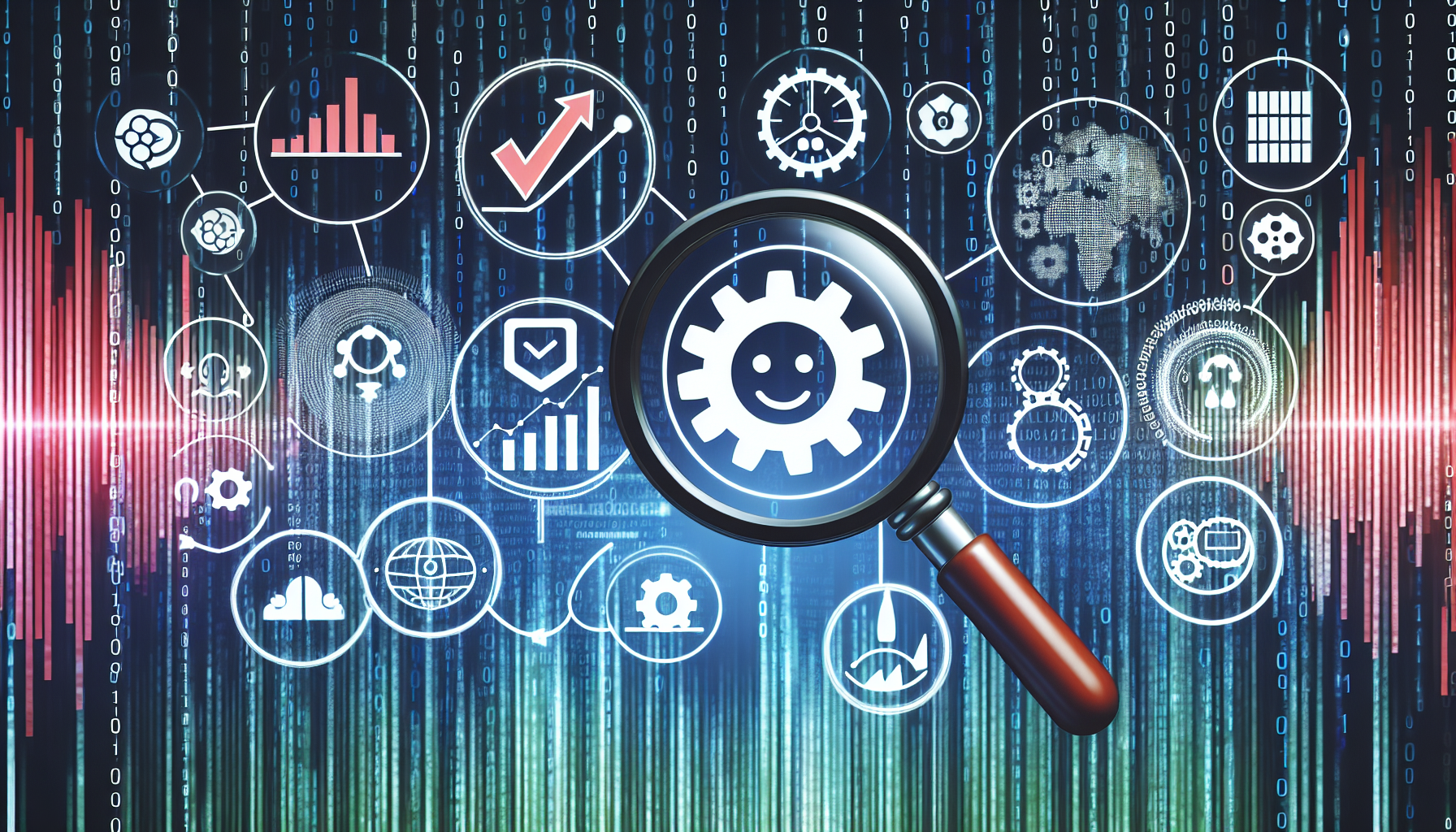
Creating a Digital Roadmap
The path to digital transformation for manufacturing companies starts with developing a clear strategy and a detailed digital roadmap. This process involves evaluating current operations, pinpointing areas that need improvement (especially manual processes), and setting realistic, measurable goals.
Taking a phased approach is key. Begin with small, impactful projects—quick wins—that showcase value early on. This helps build momentum and gain support from stakeholders throughout the organisation.
A great first step is to assess your current digital maturity. Use our digital scorecard to benchmark your progress and identify areas for growth. This structured approach ensures a strong foundation for a successful digital transformation journey.
Technology Selection
Key technologies like IoT, AI, and robotics are driving digital transformation in manufacturing today:
- IoT enables real-time monitoring and predictive maintenance, keeping operations running smoothly.
- AI delivers valuable insights for smarter decision-making and process optimization.
- Robotics automates repetitive tasks, allowing human workers to focus on more complex and strategic activities.
When combined, these technologies create a streamlined, efficient, and highly connected manufacturing ecosystem.
Workforce Transformation
Equally important to digital transformation is the evolution of the workforce. Employees need new skills, including digital literacy, data analysis, and the ability to collaborate with advanced technologies. Providing training and development programs helps ensure your team is prepared to succeed in a technology-driven workplace.
Overcoming Objections to Digital Transformation
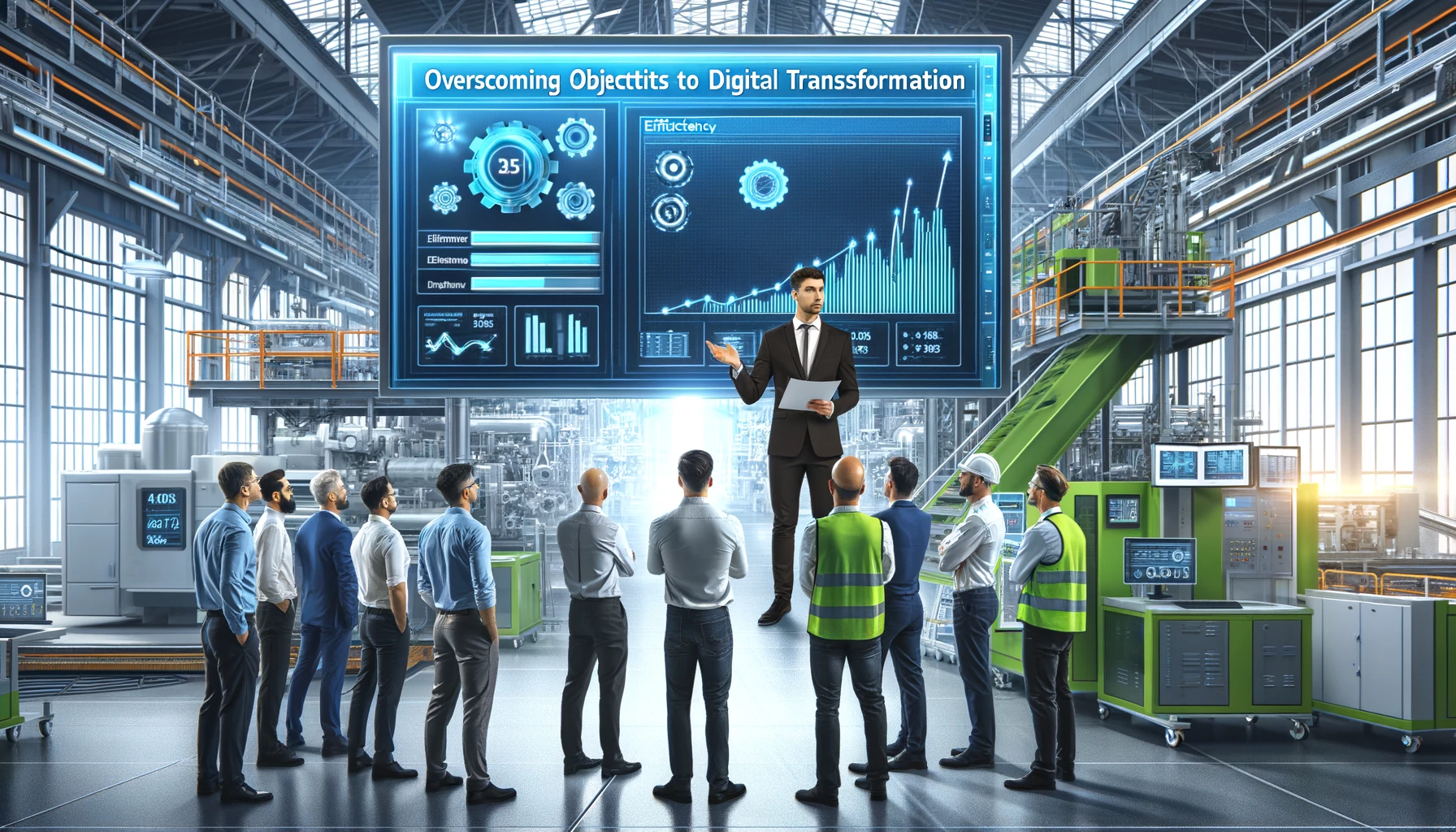
Addressing Cost Concerns
Investing in digital technologies may feel overwhelming at first, but the long-term benefits far outweigh the initial costs. Improved efficiency, reduced downtime, and better product quality all contribute to a strong return on investment (ROI). Additionally, with technology costs dropping significantly, digital tools are now more affordable and accessible for manufacturers of all sizes.
Managing Change Resistance
Change can be challenging, but involving employees early can make all the difference. Clearly communicate the benefits of digital transformation and include them in decision-making. This collaborative approach fosters a culture of innovation and adaptability, ensuring everyone is aligned with the digital strategy for success.
Managing Legacy systems
Managing legacy systems and addressing technical debt are key challenges in digital transformation. A balanced approach is essential, weighing the business value of current systems against the benefits of adopting new digital solutions.
Start by conducting a thorough audit of your IT infrastructure to identify which systems are critical to operations and which can be retired or upgraded. Focus on reducing technical debt, especially in areas that limit agility or pose security risks.
An incremental approach to modernisation works well. For example, using APIs to integrate legacy systems with new technologies allows for gradual upgrades without disrupting operations. At the same time, fostering a culture of continuous learning within the IT team ensures skills stay relevant and aligned with the latest digital advancements.
Clear communication across departments is equally important. Keeping everyone informed about the digital transformation journey helps align business and IT strategies, creating a unified and effective approach to overcoming the challenges of legacy systems and technical debt.
Mitigating Security Risks
Digital transformation brings new cybersecurity challenges. To address these risks, manufacturers should follow best practices such as conducting regular security assessments, implementing strong cybersecurity measures, and providing employees with proper security training. Prioritizing cybersecurity helps protect digital systems and secure sensitive data.
Actionable Steps Towards Digital Transformation
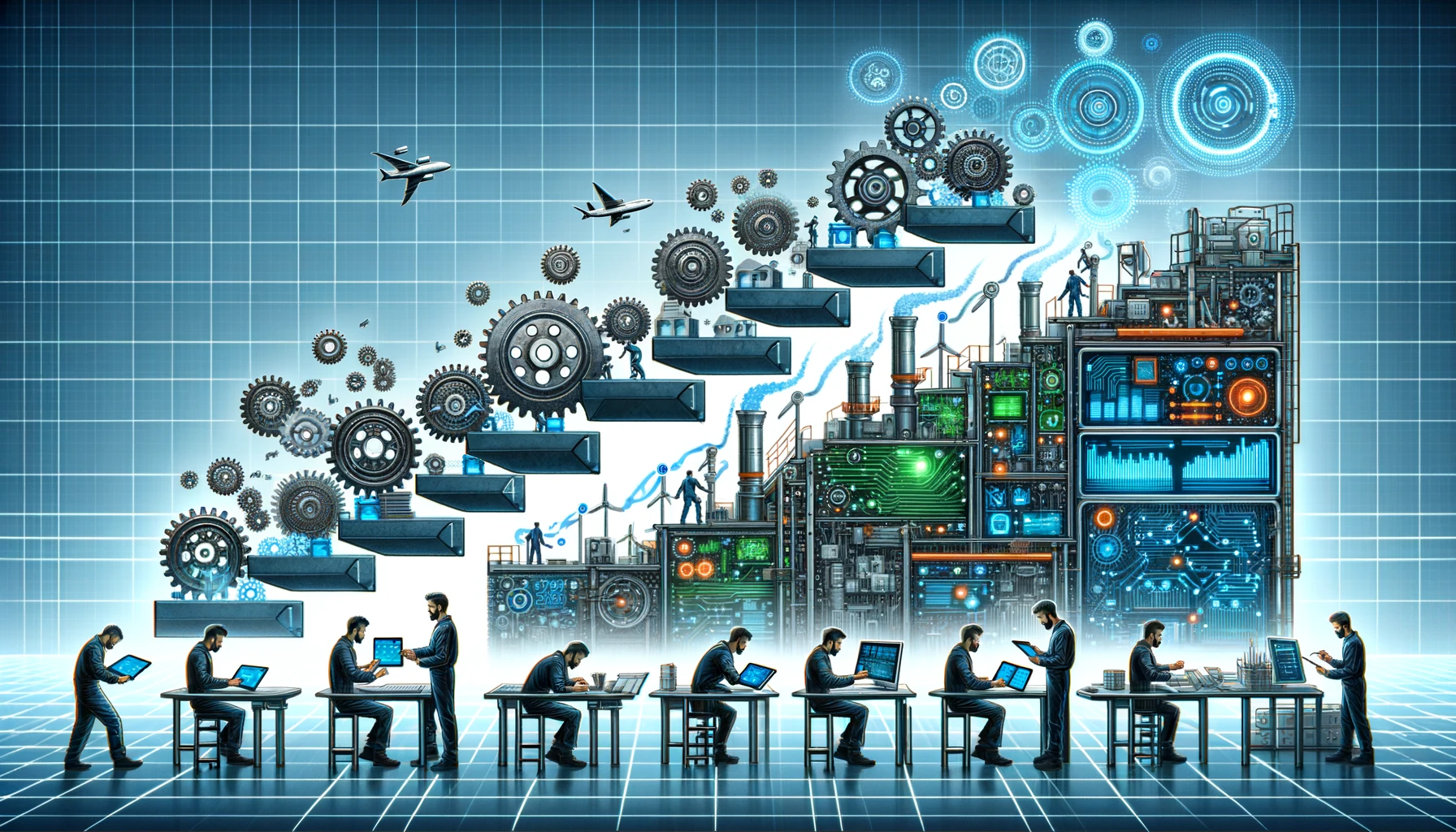
Starting Small
Start your digital transformation journey with quick-win projects that focus on specific areas for improvement. These smaller initiatives allow you to test new technologies, refine your approach, and demonstrate tangible results. This builds confidence and support for broader transformation efforts.
Common quick-win projects include:
- Training staff on how to better use existing systems.
- Adding a reporting layer to improve visibility and decision-making.
- Simplifying and standardising business processes for greater efficiency.
- Implementing a Software-as-a-Service (SaaS) solution for quick results.
- Integrating systems to eliminate duplicate data entry and improve workflow.
These quick wins provide meaningful benefits without the need for a full-scale transformation. Starting small helps build momentum and sets the foundation for larger, more impactful changes.
Choosing the Right Strategic Partner
Choosing the right technology provider is essential for a successful digital transformation in manufacturing. Look for partners with a strong track record of implementing digital solutions specifically for manufacturing. Their expertise and tailored services can help you navigate the unique challenges of the industry with confidence.
Embracing Continuous Learning and Adaptation
The digital world is constantly changing, and staying competitive means embracing continuous learning, adaptability, and innovation. Foster a culture of ongoing education in your organization and stay open to new technologies and methods that can improve your operations.
The Future of Manufacturing
The future of manufacturing is undeniably digital. Manufacturers that embrace digital transformation will lead the industry, setting new standards in innovation, efficiency, and competitiveness. While the journey may seem daunting, the rewards—higher productivity, better product quality, and greater adaptability to market changes—make it a worthwhile investment.
Smart manufacturing represents the peak of industrial innovation. It integrates advanced technologies like IoT, AI, ML, big data analytics, and robotics to create efficient, automated, and self-optimizing production environments. By leveraging real-time data, smart factories can predict maintenance needs, adjust to changing production demands, and optimize resource use. The result is reduced downtime, higher productivity, and consistently improved product quality.
Conclusion
Digital transformation in manufacturing is no longer just a trend—it’s a strategic necessity for staying competitive in a fast-changing industry. By challenging misconceptions, adopting new technologies, and fostering a culture of innovation, manufacturers can achieve greater efficiency, productivity, and growth. The future of manufacturing is digital, and now is the time to act.
Start your transformation journey by assessing your current processes, exploring new tools, consulting with experts, or attending workshops on digital strategies for manufacturing. Embracing change and leveraging the power of digital technologies is the first step toward revolutionising your operations and securing long-term success.